In PCB (Printed Circuit Board) assembly, the layout optimization of components is a key step to ensure the performance, reliability, manufacturability and maintainability of the circuit. The following are detailed suggestions for optimizing the layout of PCB components:
First, the general principle
Functional zoning:
Divide the circuit according to its functional blocks, and place components with the same or related functions together to facilitate signal flow and power management.
Avoid mutual interference among components with different functions. For instance, separate digital circuits from analog circuits and high-frequency circuits from low-frequency circuits.
Signal integrity
When laying out, consider the direction and length of the signal lines, and try to shorten the length of the key signal lines to reduce signal delay and interference.
For high-speed signal lines, differential signal transmission is adopted, and the length of the differential line pairs is shortened as much as possible, keeping the line pairs parallel and of equal length.
Heat dissipation considerations:
Components with high thermal power consumption should be placed in positions conducive to heat dissipation, such as near ventilation openings or heat sinks.
The heating elements should be evenly distributed to avoid local overheating.
Manufacturability and maintainability:
The layout of components should facilitate soldering, testing and maintenance.
Leave sufficient space for the operation of test fixtures and maintenance tools.
Second, specific layout techniques
Start with the big and then move on to the small; start with the difficult and then move on to the easy.
Prioritize the layout of important unit circuits and core components to ensure their reasonable positions and smooth signal flow.
For components that are difficult to wire, their positions should be planned in advance to avoid subsequent wiring difficulties.
Reference principle block diagram:
According to the principle block diagram of the circuit, determine the layout positions of the main components to make the signal flow direction clear and reasonable.
Convenient for debugging and maintenance:
Avoid placing large components around small ones to prevent hindrance during debugging and maintenance.
Sufficient space should be left around the components to be debugged to facilitate the connection of test instruments.
Symmetrical layout
For circuit sections with the same structure, a “symmetrical” standard layout should be adopted as much as possible to enhance the consistency and aesthetic appeal of the layout.
The orientation of components is consistent:
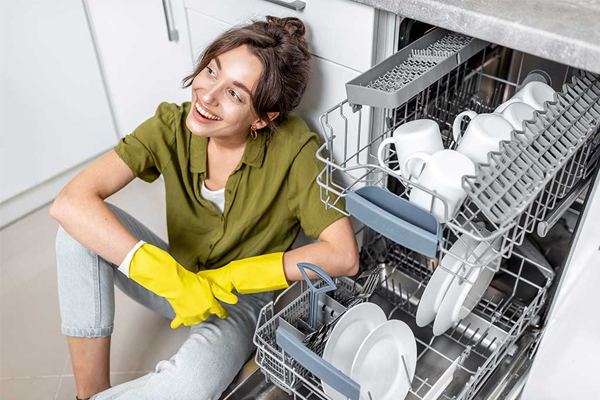
The same type of through-hole components should be placed in the same direction in the X or Y direction. For the same type of polar discrete components, efforts should also be made to keep them consistent in the X or Y direction to facilitate production and inspection.
Positioning of high-frequency components
When the frequency of the electrical signal exceeds 1MHz, special attention should be paid to the positioning of high-frequency components.
High-frequency components should be placed as close as possible to shorten the length of high-frequency signal lines and reduce signal interference.
The ground layer must be very limited in terms of expansion, and the components connected to it should be as close to each other as possible.
Layout of decoupling capacitors:
Decoupling capacitors should be placed as close as possible to the power pins of the IC to shorten the circuit length between the power supply and ground and enhance the decoupling effect.
Layout of heat dissipation components:
The heating elements should be evenly distributed to avoid local overheating.
For applications with high power requirements, heat-generating components such as voltage regulators and power operational amplifiers should be placed in positions conducive to heat dissipation, and the use of heat dissipation vias or heat sinks should be considered.
Avoid overlap and intersection:
Components should avoid overlapping and crossing to prevent short circuits and signal interference.
When wiring, efforts should be made to minimize the crossing of signal lines. If it is unavoidable, vertical crossing should be adopted to reduce signal interference.
Make space for the copper trace lines:
When placing components, ensure there is sufficient gap for copper wires to pass through, especially near components with hundreds of pins.
Avoid arranging overly dense traces in areas with a high concentration of components to prevent increasing the difficulty of wiring and signal interference.
Follow the schematic design:
Placing components by logical groups on the PCB layout as in schematic design will save time and minimize the trace length to the greatest extent.
Many components have been logically grouped according to the schematic diagram. When laying out, this grouping relationship should be maintained as much as possible.
Third, layout inspection and optimization
Signal integrity check
Use the signal integrity analysis tool to check the layout to ensure that parameters such as the length of the signal line, impedance matching, and crosstalk meet the requirements.
Thermal analysis
Conduct thermal analysis on the PCB to ensure good heat dissipation of heat-generating components and avoid local overheating.
Manufacturability inspection
Use manufacturability inspection tools to check the layout to ensure that the layout of components complies with the requirements of the manufacturing process.
Check whether the spacing of components, soldering points, vias, etc. comply with the standards.
Optimize the layout
Based on the results of signal integrity, thermal analysis and manufacturability inspection, the layout is optimized and adjusted.
Adjust the parameters such as the position, direction and spacing of the components to make the layout more reasonable and efficient.
By following the above layout optimization principles and techniques, the performance, reliability, manufacturability and maintainability of PCBS can be significantly improved. In practical applications, flexible adjustments and optimizations should be made according to the requirements of specific circuits and the limitations of manufacturing processes.